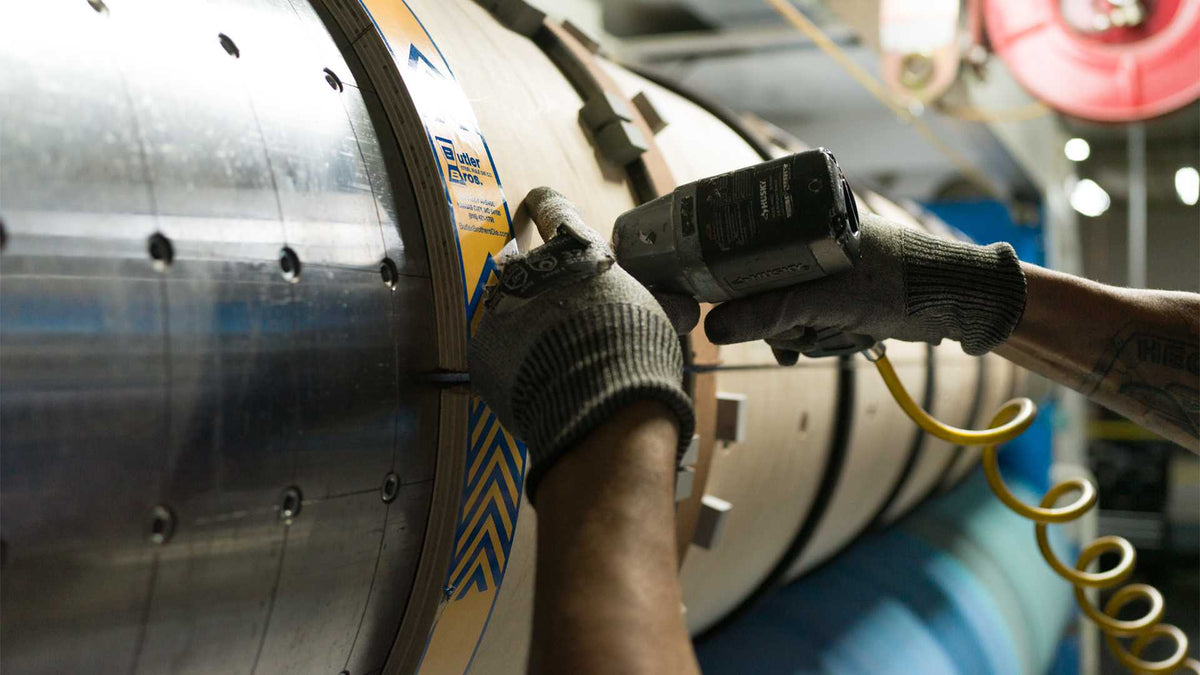
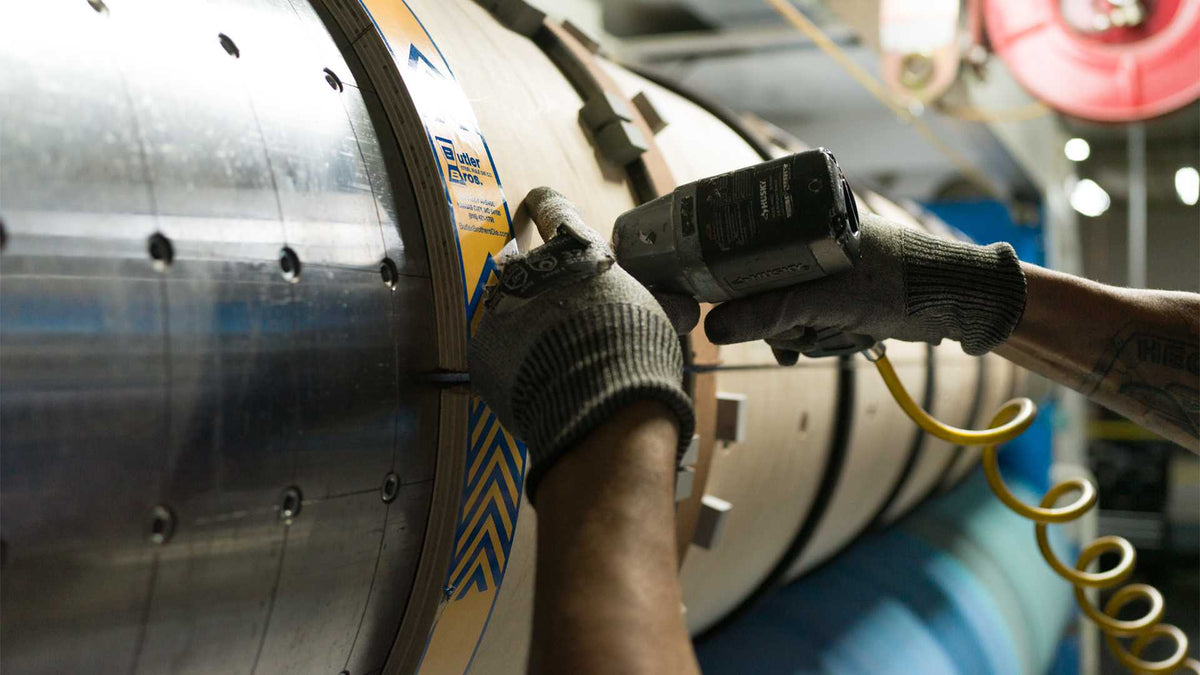
Commonly referred to as "tooling", Printing Plates and Cutting Dies are one-time upfront costs needed to produce some products in the corrugated industry. They are large up-front costs that businesses need to invest in to make their corrugated products. Cutting dies are like a large cookie cutter, and printing plates are like a large stamp.
When a new customer tries to make their first purchase of corrugated packaging or POP Displays, they will often see large line item costs. Things called Printing Plates and Cutting Dies.
Let's dig into what these two items are so you are able to make a more informed decision.
These are simply tools used for the mass production of corrugated products.
Let's dig into what these two items are to help you make a more informed decision.
Table Of Contents
What Are Printing Plates?
Printing Plates are made from metal or polymer materials. These plates are pressed into a sheet of material to give it the appearance of being printed. They print designs onto packaging in large volumes on manufacturing equipment. Almost like a large stamp, some plates can print over 1 million boxes before needing to be replaced.
The most common type of printing plates are letterpress plates, which have raised elements that transfer ink onto the substrate, creating an impression. This is similar to how you would press your finger into soft mud or clay, leaving an impression.
Ink is then rolled over the plate, transferring the ink through the image that has been etched onto the print plate.
Time Needed To Create Printing Plates
Typically, these can take anywhere from 6 to 8 weeks to produce. They are made by special manufacturers, not corrugated manufacturers. So all of these vendors must work together to serve the customer's needs.
Flexographic Printing
Flexographic printing plates are photopolymer plates that are flexible and are used in flexo printing to transfer ink and pictures on a flexible substrate like paper or film. The printing plates are an important part of the flexographic printing process, and the quality of the printed image is heavily influenced by the flexo plates used.
The flexo technique is well-known for its ability to print on a variety of flexible substrates and for the plates' ability to be reused over millions of impressions. The plates are created in relief, which means that where the picture has been exposed, the print surface is elevated.
After the ink is placed on the plate, the only region that touches the substrate is the plate surface. The ink does not come into contact with the etched or relieved regions.
Flexo plates were originally composed of rubber, but they are now constructed of photopolymer material in sheet form, which distinguishes them from offset printing's fixed metallic printing plates.
The plates are flexible enough to wrap around print/plate rollers that are cylindrical.
Lithographic Printing
Other types of printing include lithographic plates where images are etched onto metal plates that reproduce high-quality imagery with precise line definition at very high speeds.
Lithographic plates are a very economical solution for printing high-quality images on substrate materials.
High-Speed Digital Printing
What's special about this printing method is there are no printing plates. Digital Printing has ink ready to print in the machine and combines as needed. That takes a huge cost out of the equation, and it helps speed up the production process.
Creating Printing Plates
Today, printing plates are made in a variety of ways depending on the vendor.
Traditional Method
A laser imagesetter exposes the appropriate picture onto a film negative. It is then put directly on the surface of the unexposed plate material and kept in place by a vacuum cover.
The picture is then fixed into the polymer substance by exposing the plate and film to UV light. UV light can only travel through the transparent regions of the negative film, allowing the UV rays to change the molecular bonding in the photopolymer substance.
The plate is then mounted to an oscillating platen and immersed in a washout tank after appropriate exposure time. Depending on the kind of plate material, the washout solution might be either water or a solvent.
A washout brush then removes the unexposed parts of the polymer from the plate base. The waste polymer is dissolved in the washout solution, which is subsequently processed for solvent reclamation and recycled.
After the washout, the plate is placed in a hot air drier to evaporate any excess water or solvent, leaving a dry plate. Finally, a post-cure utilizing both UVA and UVC lamps is necessary, and the completed plate is ready to use.
Digitally Created
Direct 'computer-to-plate' technology is now used to expose the majority of flexo plates (CTP). The film negative is pre-laminated onto the photopolymer sheet in this process. It allows both layers to be exposed in the same piece of equipment.
A computer directs a laser to expose the negative layer first, followed by the photopolymer being exposed to the UVA light source. When compared to the usual procedure, this exposure technique creates a higher-quality plate. The exposed plate is subsequently treated using the above-mentioned washout procedure.
Thermo Processing
This process removes the need for water or solvent during etching. The photopolymer's unexposed portions are effectively melted and removed using a mechanical process. It involves heat treatment and a series of revolving rollers.
This procedure is considered to be less harmful to the environment than traditional plate washing processing.
Related: Litho vs Digital Printing
What Are Cutting Dies?
Cutting Dies are large pieces of tooling made of blades, plastic, rubber, and more. They are applied to the manufacturing equipment that cuts corrugated at high speeds, and are the negative of the desired box shape. This tooling typically lasts years and is good for multiple uses.
Cutting dies are not normally required for basic shipping boxes (RSCs, HSCs, FOLs, OPFs, and 5PFs), pads, or scored sheets. That's because these packaging styles are so common that most manufacturers have tooling already. Anything that goes beyond the capability of normal box-making technology, on the other hand, does.
Mailer boxes, POP displays, custom inserts, boxes with cutouts and windows, and most trays fall within this category. A cutting die charge will be added to your quote for these goods. This is a one-time cost to purchase the die, which may be used on subsequent orders.
Time Needed To Create Cutting Dies
It typically takes 6-8 Weeks to create cutting dies for manufacturing. This is done by special vendors that must work together with corrugated manufacturers to service the customer.
Breaking It Down
Cutting dies consist of three components: the die block, a slug, and a backer board. The die block is the metal piece that creates the shape, the slug is an unfinished part of the shape left behind after cutting which can be recycled later to make new dies, and the backer board consists of two material sheets laminated together with a wood core in between them giving it strength.
What Are Die Cut Boxes?
Die cut boxes are corrugated cardboard boxes that may be customized to meet any shape, size, or demand. Die cut boxes are made from simple sheets of corrugated material and are cut using a machine called a die press (or die cutter).
Engineers or design professionals design the die cut boxes first, then the die press is set up and equipped to cut the cardboard. After the boxes have been cut, distinctive visuals such as product information, warnings, or branded logos may be added to personalize them further.
Save Money With Die Cut Boxes
Because fully customized boxes are generally somewhat more costly than conventional sized and shaped boxes, the concept that they might save your firm money seems counterintuitive. Die cut boxes, on the other hand, can save you a lot of money in the long run.
Any unused space in a shipping truck, rail car, or airplane cargo bay is nothing more than a waste of money when items are delivered. Despite the fact that most carriers ship by weight rather than volume, wasted space means fewer goods are transported with each load.
Die-cut boxes are tailored to suit your product more precisely than normal shipping boxes. Not only does this reduce the amount of wasted space during shipment, but it also eliminates the need for additional packing materials, such as foam packaging peanuts, to cover the empty space; another cost-cutting element.
Related: Custom Shipping Boxes vs Stock Boxes
While the cost of a larger load is likely to be higher, your products may be shipped in fewer loads.
Order Custom Packaging And Displays Today!
Print Plates & Cutting Dies are tools corrugated manufacturers use throughout North America to produce their products. Without these tools, it would be impossible for any corrugated packaging manufacturer to produce at high speeds or low costs.
As you can see, there are several uses for printing plates and cutting dies in the world of corrugated boxes. Talk with our team if you have any questions about how these tools are used or what is involved in their creation.
Contact us today to start a new packaging or display project.