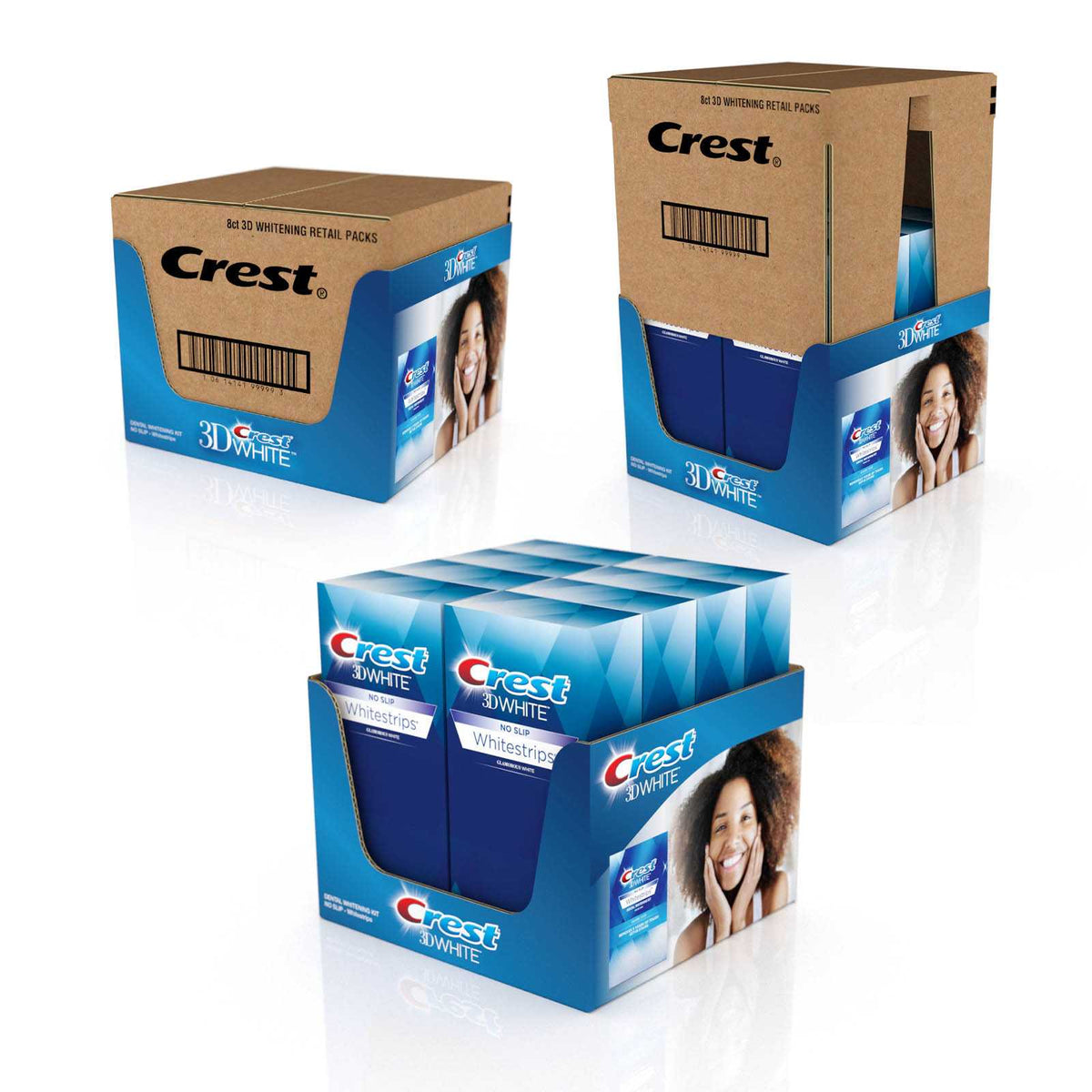
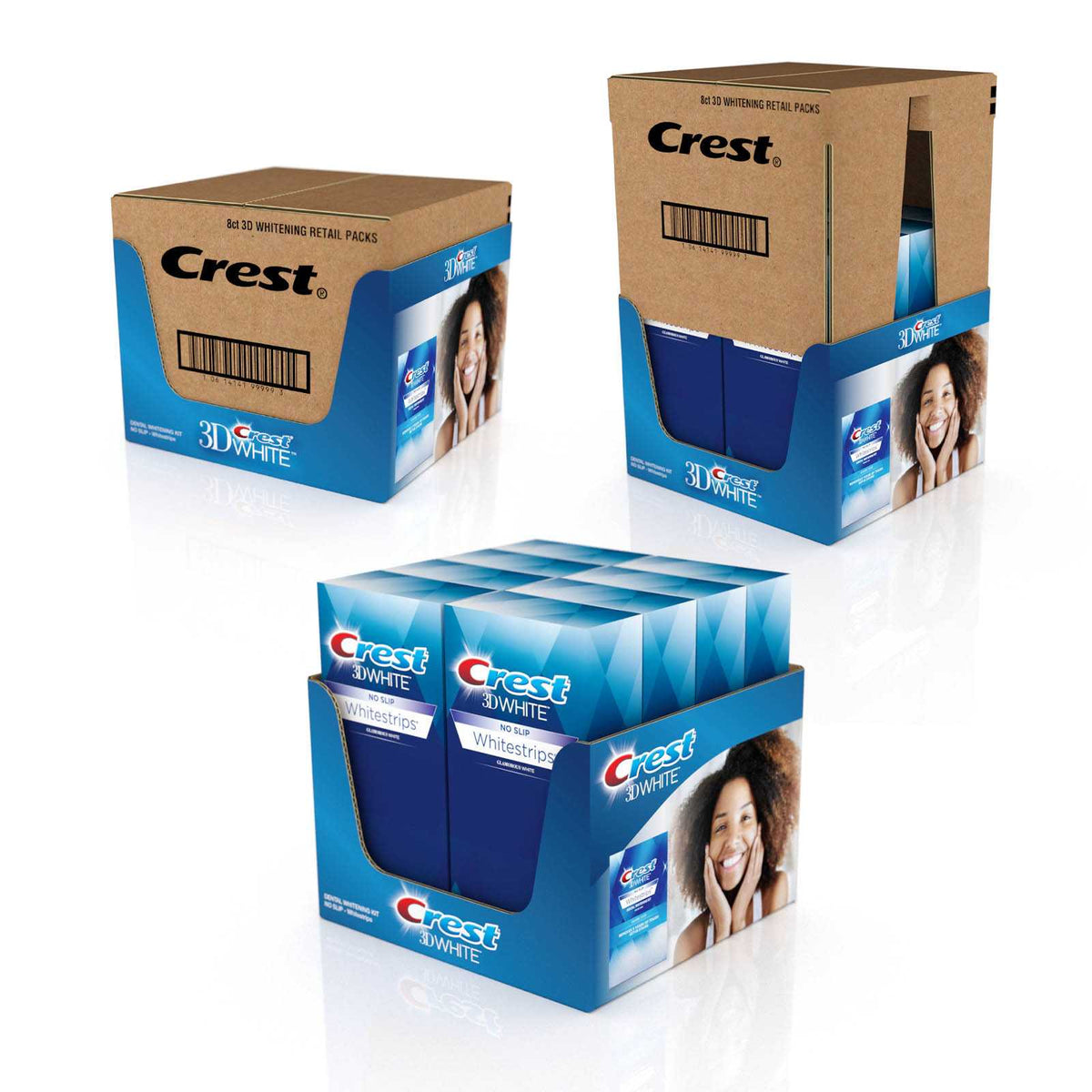
The Complete Guide To Shelf-Ready Packaging
Looking for Walmart-ready Shelf-Ready Packaging? Or is another retailer asking you for SRP / RRP?
We see this a lot: simple, non-custom, Shelf-Ready Packaging that gets the job done. How can you expect to hit your sales target if you don't invest in your presentation at the store?
You have a great product, but you left out one thing - a plan to execute at the top level at retail! Shelf-ready packaging is a great way to grab your customers' attention at retail and solve the problem of slow restocking. Working with a Packaging Manufacturer can significantly benefit you and your brand.
It's an easy thing for most brands to overlook, but this is precisely the issue we aim to solve.
SRP or RRP has become a requirement for entry and an essential element of leading retailers’ strategies.
If you want to establish a new relationship, you should start by creating an appealing and functional SRP design.
We help upgrade brands from plain to premium, take advantage of all the latest technical and marketing innovations to create new designs, and, more importantly, increase your sales.
Bringing new packaging ideas to life can be a challenging task. That’s why we created this guide to walk you through each step. Shelf-ready packaging is being demanded by retailers more every day.
Talk with our team today about your next Shelf-Ready Packaging.
Why switch to Shelf-Ready Packaging?
Shipping products in their packages reduces and eliminates repacking because products are shipped in their own packages. That means material, weight, shipping, and other costs are reduced!
Shifting to SRP means you can innovate your packaging to become more cost-effective and, thereby, more attractive to retailers and consumers.
How Shelf-Ready Packaging helps your product
- Identify: Retail employees are able to clearly see a product name in a storage area and put it out on the store floor.
- Opening: Packages need minimal or even no equipment to open. Specially engineered packages eliminate the need for knives or box cutters.
- Replenish: Restocking is faster and is now a one-touch process.
- Shopping: Customers can quickly identify products on shelves and pull them off the shelf.
- Dispose + Recycle: The packaging is easy to remove, dispose of and recycle.
- Sales: Increased sales through impulse purchases.
- Protection: Reduce damage during shipping due to strength and stability.
- Presentation: Better customer perception as products are easier to find with improved availability
- Supply Chain: Reduced storage space and transport costs from supply chain optimization
Table Of Contents
Step 1: Determine Your Shelf-Ready Needs
- What type of product do I have?
- Are there new innovations I can implement?
- What dimensions do I need?
- How many units do I need?
- How can this be an extension of my brand?
A) What type of products do I have?
The type of packaging you need will vary depending on your product. This will be based on the size, shape, and weight.
If you have a fragile product, you would need to consider a structurally safe solution that includes cushioning.
B) Are there new innovations you can implement?
Getting ahead of your competition is important. You should research or find a trusted packaging partner who can confidently update you on the latest innovations in the marketplace.
There are so many new, exciting ways to reach customers, and if you're creating a new packaging design, you should include some!
Related: 7 Design Tips For Costco Packaging.
C) What are your dimensions?
Start by measuring your product's height, width, and length and everything you plan to put inside the box. Then, consider the type and size of any protective packaging inserts you plan to use. This will determine the size of the box you need.
Pro Tip: Minimize your box as much as possible. This will allow the product to fit safely and avoid any shipping damages. Most importantly, you will reduce your costs and carbon footprint.
D) How many units do you need?
How much do you plan to sell? Do you need 100 units? 500? 1,000? 10,000? Will you need recurring orders? This will directly affect your costs; the more you order, the better the deal you can get.
Related: 7 Design Tips For Walmart Packaging.
E) How can this be an extension of your brand?
This is a critical part of Step 1. While there are options for simple brown, white, or plain designs, treating your SRP as an extension of your brand will do wonders to increase sales.
Using your branding, colors, fonts, and other aspects on the package will tell the customer “who you are,” - not to mention that you’ll definitely stand out.
The entire concept of SRP is that the teams in charge of restocking the shelves can do it faster than ever before!
Step 2: Establish Your Budget
A successful Shelf-Ready Packaging program needs a budget that considers the economics of the entire process.
You should consider your product's price, profit margin, anticipated sales, and the length of time you expect your Packaging to be in place.
Setting a budget or at least a range for your Shelf-Ready Packaging helps the process not become inefficient or aimless.
Your budget should include the cost of Packaging Supplies and Shipping Boxes.
If any packaging fillers are required, you need to account for them. You can also include a Contract Packager to help with fulfillment or assembly.
By using a company like Bennett, you get Turnkey Solutions that help you minimize costs.
Volume purchasing
As with most printed products, you only really get a good value at high purchase quantities due to the economics of scale. If you don’t buy in bulk, each package will add an unreasonable amount of expense to each shipment.
If you do buy in bulk, you will not only be putting more money up front for production but also for storage, transportation between warehouses, and handling. Digital allows you to have complete flexibility for this.
Related: Get Products On The Shelf With SRP
The higher the sales price of your product, the more you should consider investing in your Shelf-Ready Packaging.
Step 3: Designing Shelf-Ready Packaging
What elements of your brand need to be seen immediately?
- Your logo and tagline
- Brand colors/fonts
- An image of your product
- Information Architecture/company story
Next, consider how you want to display your product.
- Inside a branded box in separate packages
- On a shelf tray with a removable top
- On a reusable plastic tray
- On a merchandising unit/display
Stackable Design
A stackable design should be your biggest priority. One of the best goals to achieve is a shelf capacity of two cartons per SKU.
Having two cartons per shelf will make restocking faster! That means no more downtime. Consider the ability to have cartons placed deep, stacked, or adjacent.
Related: 5 Design Tips for SRP
Here are some other SRP tips:
- Try simple changes in package configuration. This is key to achieving better shelf and pallet optimization.
- Marketing and engineering need to work together to create SRP that consumers find easy to shop. The best SRP helps consumers quickly identify the product, grab it, and move down the aisle.
- The best SRP will help you reduce materials. Using no shrink film, staples, excessive tape, or glue.
- Stand-up pouches are some of the best in class SRP. They offer flexibility and convenience while being visually appealing and structurally stable.
- Wal-Mart has “Easy to Identify” criteria, ensuring that all branding is visible on a minimum of four sides.
- You should include opening instructions for personnel to be compliant with most retailers.
- If your plan involves multiple retailers and markets, include time for alternate designs to be compliant.
Pro Tip: If you’re not a designer and don’t have a design team - we provide access to our award-winning in-house team in Creative Services.
Step 4: Choose a Printing Style
Choosing a printing option is more than simply looking at cost factors. The technology has been changing over the years, and while some older methods are still proven and effective, newer methods have introduced new ways to attack the marketplace.
Here are three printing options to consider:
Lithography Printing
When it comes to commercial printing needs, lithographic printing is the most used solution. And it’s great if you are creating a single design to print over and over without much customization.
One of the main issues is the upfront costs for the printing plate and the lead time for the project.
If you choose Litho, that means you’re committing to waiting and a portion of your budget before you even get your first box.
If you are looking for a high-volume production run of a single design, this is the way to go.
High-Speed Digital Printing
Bennett's digital presses are game-changing for the custom retail packaging industry.
While other companies might tell you that Digital isn’t competitive when running large orders, what they aren’t telling you, is that with Digital, you can run a variety of designs without needing to pay for or wait for new printing plates to be made.
Digital has been growing, but only a few brands have taken advantage of this enormous opportunity.
Imagine creating regional messaging, designs for different stores, seasonal or product variation sizes - all without additional costs.
We were the first to invest in a high-speed, single-pass, direct-to-corrugate, 6-color digital press in North America. If you'd like to learn more, you can check out our page on Digital.
Related: 5 Digital Printing Tips For Shelf-Ready Packaging
Flexography Printing
Flexographic printing will bring your printing costs down, and tooling costs are typically lower. It has a fast turnaround time and can use both water and oil-based inks.
But, compared to Lithography and Digital, Flexography has a noticeably lower printing quality.
It cannot create photo-quality images, and smooth colors or gradients will have visible banding.
The colors aren’t as vibrant or crisp as the other two options, but this printing format is inexpensive. It also doesn’t require much attention to detail and can be produced at very high speed.
Designing With Digital
Here are some design tips to create an effective Shelf-Ready Packaging from the ground up:
Information Architecture
Messaging needs to be clear and motivated. What should your customers know as they pass by the Packaging? What can they see from across the store? Keep it concise and focused! Only the important benefits should be included here.
Shelf-Ready Product Showcase
Shelf-Ready Packaging is all about bulk inventory and showcasing sales items for impulse buys. These are a great way to collect things like DVDs, toys, electronics, and other products in a colorful pile to draw in customers.
Color Science
Each color speaks to the customer on a different emotional level. That's something all designers know. Why not use that on the store floor? Here's an actual opportunity to put that knowledge into practice and create something that matches your brand in a powerful way.
Match Your Brand Colors
Most manufacturers claim they will match your brand colors accurately, but they're not actually equipped to do that. We have some of the best printing capabilities in North America and promise we can actually match with 100% accuracy.
Step 5: Do You Need Paper Coating?
A coating can be applied to complete your packaging’s look - while offering additional protection and even enhancement.
Matte Lamination
While the overall effect of matte laminated surfaces is understated and elegant, it creates a noticeably high-end and sophisticated feel to your packaging.
Gloss Lamination
This provides a beautiful shine, vibrancy, better image contrast, and a more vibrant depth of color. Gloss lamination even offers better protection against things like moisture and dust.
AQ Coating
AQ Coating is a clear, water-based coating capable of fast drying. It’s environmentally friendly, making it an excellent choice for food, household, and fast-consuming products. It has a very faint gloss finish compared to UV coating and lamination.
UV Coating
UV Coating can create a similar look to lamination, but the difference is that UV is applied directly to the material. Packages are UV-coated using a flood or spot application. Spot coating is applied to one area of the package, while flood (or overall) indicates a coating applied to the entire package.
Spot UV is generally screen coated in thick amounts for maximum visual "pop" and rub resistance. While flood is usually roller-coated in relatively smaller amounts.
Varnish
Varnish increases the perceived quality of the product. However, it offers a lower degree of protection compared to aqueous and UV coating.
They are also susceptible to yellowing over time. Varnishes are also not particularly eco-friendly. This is the least popular option.
There are other options, but these are the most popular.
Related: Printing Coating Options
Step 6: Do You Need Special Finishing?
Consider enhancing your packaging by adding a more impactful look & feel. You can include a variety of special processes to create a more eye-catching design.
Foil Stamping
Perception is everything. A product with a foil-stamped package can have a higher perceived quality and value than one in a standard package. Foil also draws attention - which can make your product stand out among a crowd of competition.
Spot UV
Similar to UV coating, but this is applied to a specific area of the packaging, rather than coating the entire surface. This is to allow for these areas to be overprinted afterward, as overprinting will not be successful on areas with a UV varnish.
Embossing + Debossing
This will add dimension and depth to your packaging. Embossing and Debossing a printed sheet creates a raised (embossing) or lowered (debossing) area. It is formed using male and female molds or dies.
Window Cutting
Small windows can allow consumers to see the product inside and can even allow the consumer to touch and use the product. Toy packaging often uses windows to allow consumers to press a button or interact with the toy.
Step 7: Creating a Dieline
Now that you have your design in place, it’s time to transfer it to the structure template, a.k.a, the dieline.
There are a few dieline and artwork preparation and requirements that need to be noted by your designated designer, even if your artwork is done and ready to go.
If you do not have a designer, then your packaging company will take care of this for you.
Dielines
A dieline is typically created on a computer using a design tool such as Adobe Illustrator, Artioscad, or Adobe InDesign. Measurements need to be precise to save time and money.
Step 8: Preparing The Artwork
Working with your packaging partner, you will deliver high-resolution quality artwork for printing. It’s best to speak directly to the company you are working with to determine the exact specifications for their CMYK printing.
At Bennett, we offer access to our award-winning Creative Services to help you design, prep, and deliver all your artwork to our manufacturing teams - and ensure your project details are correct every step of the way.
Pro Tip: Need more clarification on preparing your artwork? Reach out to Bennett if you need help with any of your designs!
Step 9: Creating Prototype Shelf-Ready Packaging
You should always request a prototype box to confirm the structure and printing for final production, especially if you have a very large order.
Once the prototype is created, it can be delivered in person or via mail.
We have an array of equipment in our Creative Services Department that will match the exact quality of our High-Speed Digital Printers to allow you to quickly get prototypes - and move your project along to production.
Step 10: Production + Shipping
Once you finalize everything, your product packaging is ready for production. You can sit back, relax, and wait for the arrival of your packaging!
Receiving your shipment all depends on your requested timeline, the package size, the delivery method, etc.
It is different depending on your situation, but your account manager will keep you up-to-date with the production and shipping process, ensuring that you are always on track.
Pro Tip: If you need to order on a consistent basis, speak to a packaging specialist to map out your inventory expectations and schedule. This will make maintaining a healthy inventory flow easier and allow the manufacturer to know exactly when you need it.
Supply Chain Solutions
Once your Packaging design is locked and production is ready, you must create a Supply Chain plan. You should consider the entire process, from manufacturing to storage to retailer delivery, etc.
Key Questions:
- Will your Packaging be shipped fully assembled or KDF?
- What is the weight of your Packaging with your Shipping Box and Supplies?
- Where will you store your Packaging?
- What is the cost for Packaging Supplies?
- Fulfillment costs, if any?
- How will you account for returns?
Key Things To Keep Track Of
Track if you have enough packaging to meet demand. It’s crucial to keep a tight inventory of the packaging you have at your fulfillment center and whether it is enough to meet the season's demands.
Did you ever run out and have to purchase more? Did that incur any delays and costs?
Did you have a surplus? Was it of only certain sizes?
Try to keep track and keep packaging inventory levels in line with demand.
Record breakage
Were your shipments kept safe? This is the priority for any fulfillment center. You should set a tolerance level for the amount of breakage you can absorb, then track whether you are meeting that goal.
If you aren’t, you should consider adding more packaging filler or using a different carrier.
Bennett Makes Shelf-Ready Packaging
Bennett is a premier packaging and retail displays manufacturing company striving to protect and promote our clients' products with customized corrugated solutions. When you work with us, you’re part of the family. We will partner with you every step of the way.
With our fully integrated design-to-delivery process, we can be the single supplier source. We are an award-winning manufacturer of virtually anything corrugate. We offer everything from plain brown shipping boxes to sophisticated, high-graphic printed point-of-purchase displays and everything in between.
Talk with our team today about your next Shelf-Ready Packaging
Frequently Asked Questions
What is Shelf-Ready Packaging?
Shelf-Ready Packaging is designed to organize products on the shelf, and aid in quickly restocking at retail. It incorporates your business’s logo, brand colors, copy, and message on the outside (and inside) of the box. This helps your brand stand out in stores.
Where can I order shelf-ready packaging?
Bennett offers a wide variety of shelf-ready packaging boxes, including folding cartons, mailing boxes, and shipping boxes. No matter what kind of product you have, or box you need, we can make it. Just Contact Us and we’ll get back to you ASAP!
What SRP style is best for my product?
The style of packaging chosen for your product depends on a number of factors. This includes the size, shape, weight, and fragility of your product - and even your target market. At Bennett, we can offer the full spectrum of styles that will take your brand from plain to premium.
What Printing Styles do you offer?
We are able to produce Litho, Flexo, and specialize in Digital. We were one of the first manufacturers to invest in Digital Printing, and that’s put us ahead of the curve. Typically customers think Digital is only useful for small runs, but Digital allows you to create printing variations and create multiple runs of different targeted designs - using some of the latest innovations in marketing!